Short Description
The Pyrometallurgical Laboratory focuses on conducting research on metal extraction processes at high temperatures / high temperature metals processing, from temperatures of 200 – 2000°C. Research can be in the form of experiments in the laboratory as well as modeling and simulating high temperature processes, for example blast furnaces, electric arc furnaces, basic oxygen furnaces (LD converters), reverberatory furnaces, rotary kilns – electric furnaces, vacuum metallurgy (Ruhrstahl – Heraeus, Vacuum Tank Degassing), manufacture of stainless steel by vacuum oxygen decarburization (VOD), and others.
Information on educational and research activities
Educational activities serve as many as 8 modules for pyrometallurgical practicum, namely:
- Module 1: Use of the METSIM program package for pyrometallurgical, copper smelter, flash smelting and PS-converter applications
- Module 2: Slag
- Module 3: Aluminothermic reduction of ilmenite to produce ferrotitanium
- Module 4: Reduction of tin oxide by carbothermic reactions
- Module 5: Water model for LD-converter simulation
- Module 6: Pelletizing and Briquetting
- Module 7: Reduction of iron sand concentrate pellets and composite pellets using a coal bed reducer using the
- Istermal-Gradient temperature method
Module 8: Kinetics of limestone calcination reactions
Current research activities focus on reducing iron sand concentrates and lateritic nickel ores. In addition, research has also been carried out on the recycling of lead from used accumulators and the extraction of mercury from cinnabar. Several research titles:
- Identification of Heating Process and Coal Addition Effect to Cylindrical Iron Sand Concentrate Pellet at 600-1100°C
- Reduction Of Mixed Laterite Iron Ore and Iron Sand Concentrate Sintered at 800 – 1100°C
- Reduction of Iron Sand Concentrate Pellet by Coal Bed Reductor and Na2CO3 Additives Using Isothermal – Gradient Temperature
- Reduction of Iron Sand Concentrate Composite Pellets by Coal Bed Reductor Using Isothermal – Temperature Gradient Method
- Effect of CaO, CaF2, H3BO3 Additon and Reduction Time on Recovery of Nickel and Iron from Nickel Saprolite Ore at Temperature 1330°C
- Steel Desulfurization on RH (Ruhrstahl Heraeus) Degasser by Powder Blowing to Produce Non Grain Oriented Silicon Steel
- Prediction of slopping of molten metal and slag in the ferronickel refining process at LD-Converter
- The use of the water model to study the mixing time and the formation of sparks when exhaling gas in the ladle
- Economic study of nickel pig iron production using mini blast furnace technology
- Characterization study of lateritic iron ore at temperature 27-1200°C with and without coal reducing agent
- Study of roasting cinnabar ore with and without the addition of CaO at a temperature of 300 – 600°C
- Study of reduction of laterite iron ore from Kalimantan using a coal bed reducer at a temperature of 800-1100°C
- Study of the reduction of limonite nickel ore with coal reducing agents at a temperature of 1000-1400°C and the effect of adding CaO, CaCl2, borax at a temperature of 1350°C
- Preliminary study of the reduction of iron oxide sand concentrate pellets resulting from red mud beneficiation using a coal bed reducer using the isothermal – temperature gradient method
- Effect of oxidation of magnetite iron ore cylinder press pellets from Kalimantan on reduction using coal bed with isothermal method – temperature gradient
- Study of the reduction kinetics of iron sand concentrate pellets using a coal bed reducer at a temperature of 800-1200°C
- Study of the effect of the addition of limestone and silica sand additives on slag viscosity and lead recovery in the reduction of lead paste from recycled used accumulators
- Separation of arsenic and antimony in tin concentrates through oxidation-reduction roasting and chlorination
Documentation of Mineral & Coal Analysis Laboratory Activities
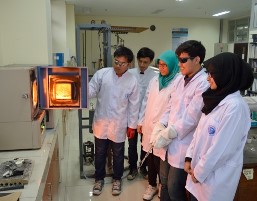
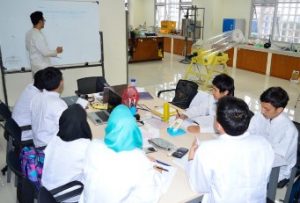
